Introduction: The Dilemma and Breakthrough of Fly Ash Disposal
Municipal solid waste incineration (MSWI) fly ash, a by-product of waste-to-energy plants, contains hazardous substances such as heavy metals (Pb, Cd, Hg) and dioxins, classified as a hazardous waste (HW18) in China’s National Hazardous Waste List. Traditional solidification-landfilling (cost > ¥300/ton in China) not only occupies land but also risks heavy metal leaching. With the advancement of "zero-waste city" initiatives, fly ash resource utilization has become critical to overcoming the "NIMBY syndrome." By converting fly ash (containing 20–30% CaO, 15–25% SiO₂, 3–8% P₂O₅) into building materials, soil amendments, and metal raw materials through technological innovation, we can achieve a value shift from "hazardous waste" to "strategic resource." This article systematically analyzes the full-chain fly ash resource utilization pathway, with the disc dryer as the technical core.
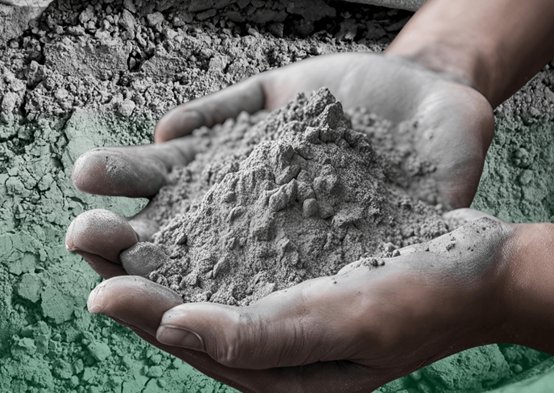
I. Disc Dryer: The Core Equipment for Fly Ash Pretreatment
1. Technical Principle
The disc dryer employs indirect heating via rotating hollow discs, transferring heat from steam to reduce fly ash moisture from 60% to 10–15% (processing capacity: 5–50 tons/hour). Key advantages:
- Energy Efficiency: Thermal efficiency > 85% (30% more energy-saving than traditional fluidized beds), energy consumption < 20 kW·h/ton;
- Environmental Safety: Fully enclosed system with tail gas condensation (dioxin removal rate > 99%), no dust leakage;
- Intelligent Control: PLC system adjusts rotation speed (5–15 rpm) and temperature in real time, adapting to various fly ash compositions (e.g., automatic cooling to prevent coking when Cl content > 5%).
2. Application Scenarios
- Stabilization Pretreatment: Dry fly ash mixed with chelating agents (e.g., DTCR) enhances heavy metal immobilization efficiency by 40%, meeting leaching limits of GB 16889-2020;
- Resource Pretreatment: Improved dry ash fluidity facilitates subsequent processes (acid leaching for metals, sintering for building materials);
- Co-treatment: Co-drying with sludge/straw (1:3 ratio) reduces costs (case in Zhejiang: cost from ¥420 to ¥280/ton).
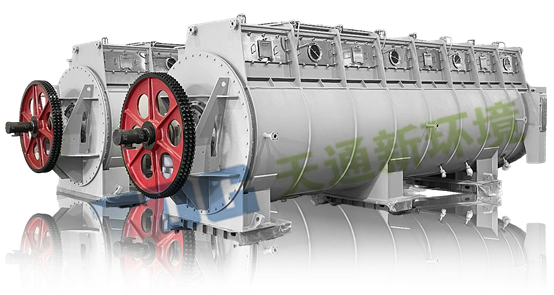
II. Four Technical Pathways for Fly Ash Resource Utilization
1. Heavy Metal Extraction: From "Toxic" to "Precious Metals"
- Process: Disc drying → acid leaching (20% H₂SO₄) → solvent extraction (P204) → electrowinning (Cu/Zn recovery > 95%);
- Case: A Jiangsu enterprise extracts 8–12% Zn from fly ash, producing 2,000 tons of electrolytic zinc annually (output value > ¥15 million);
- Value: Zinc ingots (¥20,000/ton), copper sulfate (¥8,000/ton), profit > ¥500/ton after costs.
2. Building Material Conversion: From "Waste" to "Green Infrastructure"
Product Type | Technical Parameters | Application Scenarios |
Ceramsite (sintering) | Bulk density < 800 kg/m³, water absorption < 10% | Sponge city filters, lightweight concrete |
Autoclaved bricks | Compressive strength > MU15, heavy metal leaching < GB 38223-2019 | Municipal walkways, walls |
Cement clinker substitute | 10–15% substitution (5–8% energy saving) | Cement production |
Role of Disc Dryer: Dry ash (moisture < 15%) improves mixing uniformity with aluminosilicate materials (fly ash, slag), reducing sintering temperature from 1,250°C to 1,180°C (7% energy saving).
3. Phosphorus Recovery: Filling the "White Petroleum" Gap in Agriculture
- Technology: Dry ash → washing (Cl⁻ removal) → alkali dissolution (10% NaOH) → crystallization (dicalcium phosphate purity > 92%);
- Data: 1 ton of fly ash contains 50–80 kg P₂O₅ (equivalent to 200–300 kg phosphate fertilizer, value ¥300–500);
- Standard: Meets HG/T 3275-2023 (industrial dicalcium phosphate), heavy metals (As < 10 ppm).
4. Soil Amendment: Remediating Heavy Metal-Contaminated Farmland
- Formula: Fly ash (40%) + biochar (30%) + humic acid (30%) → passivation material (pH 8.5–9.0);
- Mechanism: CaO immobilizes Cd²+ (Cd(OH)₂ precipitation), aluminosilicates adsorb Pb²+ (coordination bonding);
- Case: Cd-contaminated farmland in Zhuzhou, Hunan: soil available Cd reduced by 62%, rice Cd < 0.2 mg/kg (GB 2763-2024 limit).
III. Typical Cases: The "Fly Ash Revolution" in the Yangtze River Delta
1. Shanghai Laogang Renewable Energy Utilization Center
- Process: Disc drying (30 tons/hour) → high-temperature sintering (1,150°C) → ceramsite production;
- Output: 150,000 tons/year ceramsite (used in Hangzhou Asian Games lightweight concrete), output value ¥120 million;
- Benefits: Replaced 120,000 tons natural aggregates, CO₂ emissions reduced by 40% (vs. landfilling).
2. Zhejiang Jiaxing "Zero-Waste City" Pilot
- Model: Fly ash (dried) + sludge ash (incinerated) → soil conditioner (4% P, 25% Ca);
- Application: 3,000 mu rice fields in Jiaxing: 20% fertilizer reduction, 8% yield increase;
- Policy: Eligible for Zhejiang solid waste resource utilization subsidies (¥150/ton product).
IV. Challenges and Countermeasures: Building a Sustainable Industrial Ecosystem
1. Key Challenges
- Technical Bottlenecks: Coking in high-Cl fly ash (Cl > 8%, 15–20% occurrence), high precious metal extraction costs (> ¥800/ton);
- Standard Gaps: Lack of national standards for fly ash-based building materials (e.g., ceramsite), low market recognition;
- Collaboration Barriers: Data silos among incinerators, recyclers, and downstream users (construction firms, farms).
2. Solutions
- Technical Innovation: Develop high-temperature resistant discs (e.g., silicon carbide coating, >600°C), integrate bioleaching (acidophilic bacteria for gold extraction, cost reduced by 30%);
- Standardization: Formulate group standards (e.g., T/CAS 1234-2025 "MSWI Fly Ash Ceramsite"), promote green building material certification;
- Digital Twin: Establish a fly ash composition database (pH, Cl, heavy metals), AI algorithms optimize resource pathways (Jiaxing pilot: decision-making efficiency +50%).
V. Future Trends: From "Resource Utilization" to "Zero-Carbon Cycle"
- Technical Upgrades:
- Disc dryer + heat pump (waste heat recovery > 70%), comprehensive energy consumption < 15 kW·h/ton;
- Fly ash-CO₂ mineralization (150 kg CO₂ fixed/ton fly ash), supporting "dual carbon" goals.
- Industrial Expansion:
- High-end products: 3D printing ceramic powder (>99% purity), lithium-ion battery precursors (lithium extraction breakthrough);
- Clusters: "Incinerator-Dryer-Industrial Park" (e.g., Qingyuan Fly Ash Industrial Park, Guangdong, annual output > ¥1 billion).
- Policy Support:
- Implement the "Hazardous Waste Resource Utilization Management Measures," introduce "fly ash carbon credits";
- Pilot "extended producer responsibility," with incinerators, covering Bear the cost of fly ash resource utilization (included in waste treatment fees).
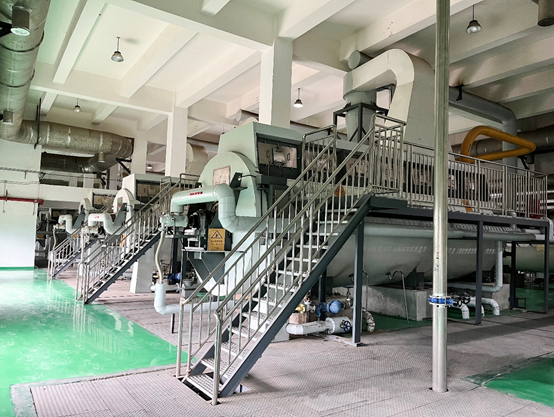
When the Disc Rotates, the City’s Future Reborn
The disc dryer is more than a dehydration device—it is the key to unlocking resource circulation. In regions with concentrated incineration capacity (e.g., Yangtze and Pearl River Deltas, 1+ million tons/day incineration capacity by 2025), fly ash is transforming from an "urban burden" to "industrial feedstock" via a "drying-sorting-high-value" chain: 1 ton of fly ash yields ¥500 in building materials, ¥300 in fertilizer, and ¥200 in metals, with over ¥1,000 lifecycle value. As technology and policies advance, this "fly ash revolution" will redefine waste management—where urban metabolism ends, the circular economy begins.